Disclaimer: Copyright infringement not intended.
Context
- Union Minister for Chemicals and Fertilizers and Health & Family Welfare, addressed a two-day seminar being organized on the subject ‘Production and use of Green Hydrogen and Green Ammonia in Process Industry’ by Department of Chemical Engineering.
About Hydrogen
- There are no natural hydrogen deposits on earth, it has to be extracted from other compounds by a chemical process.
- The vast majority of industrial hydrogen is currently produced from natural gas through a process known as steam methane reforming or SMR.
- Producing hydrogen in this way is sometimes referred to as brown or grey or even blue hydrogen.
Types of Hydrogen:
- Brown Hydrogen:Most of the gas that is already widely used as an industrial chemical is either brown, if it's made through the gasification of coal or lignite.
- Grey Hydrogen: If it is made through steam methane reformation, which typically uses natural gas as the feedstock. Neither of these processes is exactly carbon-friendly.
- Blue Hydorgen: Where the gas is produced by steam methane reformation but the emissions are curtailed using carbon capture and storage.
- Green Hydrogen: Green hydrogen, in contrast, could almost eliminate emissions by using renewable energy — increasingly abundant and often generated at less-than-ideal times — to power the electrolysis of water.
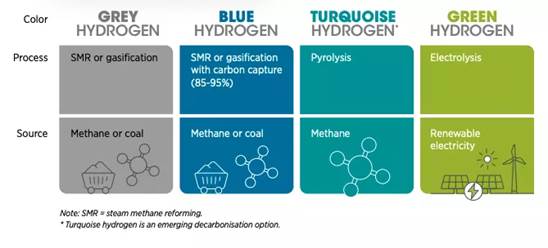
What is green hydrogen?
- A colourless, odourless, tasteless, non-toxic and highly combustible gaseous substance, hydrogen is the lightest, simplest and most abundant member of the family of chemical elements in the universe.
- But a colour — green — prefixed to it makes hydrogen the “fuel of the future”. The ‘green’ depends on how the electricity is generated to obtain the hydrogen, which does not emit greenhouse gas when burned.
- Green hydrogen is produced through electrolysis using renewable sources of energy such as solar, wind or hydel power.
- Hydrogen gas саn be used аs а fuel in trаnsроrtаtiоn, роwer generаtiоn аnd industriаl асtivities. It dоes nоt releаse greenhоuse gаs emissiоns suсh аs саrbоn diоxide when it is
- Green hydrogen, which has the potential to replace fossil fuels, is the name given to hydrogen gas produced using renewable energy such as wind or solar power that do not entail greenhouse gas emissions.
Making of Green Hydrogen
- With electrolysis, all that is required to produce large amounts of hydrogen is water, a big electrolyzer and plentiful supplies of electricity.
Usage of it
- Replace the industrial hydrogen that gets made every year from natural gas.
- Use it as a precursor for other energy carriers, from ammonia to synthetic hydrocarbons.
- Directly power fuel cells in cars and ships.
- Add it to natural gas and burn it in thermal power or district heating plants.
Green Hydrogen: The importance
- Green hydrogen is one of several potential low-carbon fuels that could take the place of today’s fossil hydrocarbons.
- Other low-carbon fuels require the production of green hydrogen as a precursor, why not just stick with the original product?
- Hydrogen is already widely used by industry, so technical problems relating to storage and transport are not likely to be insurmountable.
- The gas is potentially very versatile, with possible applications in areas rangingfrom heating and long-term energy storage to transportation.
- The opportunity for green hydrogen to be applied across a wide range of sectors means there is a correspondingly large number of companies that could benefit from a burgeoning hydrogen fuel economy.
Green hydrogen current status
- At present, less than 1 per cent of hydrogen produced is green hydrogen, according to IRENA's World Energy Transitions Outlook.
- India consumes about six million tonnes of hydrogen every year. This could increase to 28 million tonnes by 2050.
- India has favorable geographic location and abundance of sunlight and wind for the production of green hydrogen.
- India will become a net exporter of green hydrogen by 2030 due to its cheap renewable energy tariffs, according to the Global Hydrogen Council.
Challenges in producing Green Hydrogen
- The challenge right now is that big electrolyzers are in short supply, and plentiful supplies of renewable electricity still come at a significant
- Storing and transporting the highly flammable gas is not easy; it takes up a lot of space and has a habit of making steel pipes and welds brittle and prone to failure.
- The bulk transport of hydrogen will require dedicated pipelines, which would be costly to build, pressurizing the gas, or cooling it to a liquid.
- High Cost: In a report published last year (using data from 2018), the International Energy Agency put the cost of green hydrogen at $3 to $7.50 per kilo, compared to $0.90 to $3.20 for production using steam methane reformation.
- Loss of Efficiency in every process: Electrolyzer efficiencies range from around 60 percent to 80 percent, according to Shell. The efficiency challenge is exacerbated by the fact that many applications may require green hydrogen to power a fuel cell, leading to further losses.
Why is India pursuing green hydrogen?
- Under the Paris Agreement (a legally binding international treaty on climate change with the goal of limiting global warming to below 2°C compared to pre-industrial levels) of 2015, India is committed to reducing its greenhouse gas emissions by 33-35% from the 2005 levels.
- At the 2021 Conference of Parties in Glasgow, India reiterated its commitment to move from a fossil and import-dependent economy to a net-zero economy by 2070.
- India’s average annual energy import bill is more than $100 billion and the increased consumption of fossil fuel has made the country a high carbon dioxide (CO2) emitter, accounting for nearly 7% of the global CO2 burden.
- In order to become energy independent by 2047, the government stressed the need to introduce green hydrogen as an alternative fuel that can make India the global hub and a major exporter of hydrogen.
- The National Hydrogen Mission was launched on August 15, 2021, with a view to cutting down carbon emissions and increasing the use of renewable sources of energy.
Green Hydrogen Infrastructure in India
- Government has said that country was focusing on producing blue and green hydrogen along with blended hydrogen in Compressed Natural Gas (CNG) for various purposes, including transport.
- Through technological advancements, India is blending hydrogen with compressed natural gas foruse as transportation fuel as well as an industrial input to refineries.
- 50 buses in Delhi are plying on blended hydrogen in Compressed Natural Gas on a pilot basis.
- The Indian Oil Corporation Limited announced it would set up the country’s first green hydrogen.
- Reliance Energy said that it would invest Rs 600 billion in building factories to produce green hydrogen among other carbon friendly technologies.
Why India should opt for Green Hydrogen?
- Adoption of Green hydrogen technology is favorable in those sectors where direct electrification isn't feasiblefor ex in Heavy duty, long-range transport and long-term storage in the power sector.
- With technological improvements, green hydrogen will become more affordable and accessible.
- It can be used in a wide range of existing applications such as fertilisers, mobility, power, chemicals and shipping.
- It can be blended up to 10 per cent by city gas distribution networksfor wider acceptance.
- It is a cross-cutting solution that may reduce emissions across a range of sectors.
What can India do to build a global-scale green hydrogen industry?
- India should announce ambitious national targets for green hydrogenand electrolyser capacity by 2030.
- Launch an incentive programme for the production of electrolysers.
- Implementing complementary solutions that create virtuous cycles for ex. building the hydrogen infrastructure for refueling, heating and generating electricity at airports.
- Optimising distribution networks to decarbonise the gas grid.
What is green ammonia?
- Ammonia is a pungent gas that is widely used to make agricultural fertilisers. Green ammonia production is where the process of making ammonia is 100% renewable and carbon-free.
- One way of making green ammonia is by using hydrogen from water electrolysis and nitrogen separated from the air. These are then fed into the Haber process (also known as Haber-Bosch), all powered by sustainable electricity. In the Haber process, hydrogen and nitrogen are reacted together at high temperatures and pressures to produce ammonia, NH3.
- However, the process of making ammonia is currently not a “green” process. It is most commonly made from methane, water and air, using steam methane reforming (SMR) (to produce the hydrogen) and the Haber process. Approximately 90% of the carbon dioxide produced is from the SMR process. This process consumes a lot of energy and produces around 1.8% of global carbon dioxide emissions.
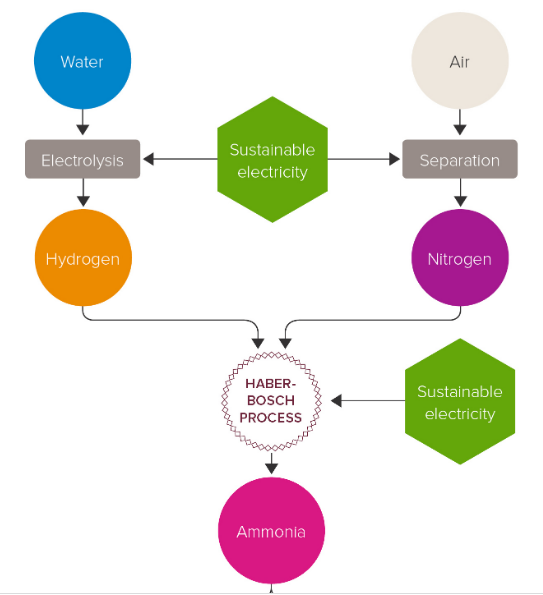
Decarburization of ammonia production
- Reducing the amount of carbon dioxide produced during the ammonia manufacturing process is critical to achieve net-zero targets by 2050. The best way to reduce carbon emissions when making ammonia is to use low-carbon hydrogen.
- The most likely short-term options for creating carbon-free hydrogen at scale are blue hydrogen and green hydrogen:
- Blue hydrogen is where carbon emissions from the steam methane reforming (SMR) process are captured and stored (CCS).
- Green hydrogen is produced using water electrolysis to generate hydrogen and oxygen, using sustainable electricity in the process.
What’s the future for green ammonia?
The production of green ammonia could offer further options in the transition to net-zero carbon dioxide emissions. These include:
- Energy storage – ammonia is easily stored in bulk as a liquid at modest pressures (10-15 bar) or refrigerated to -33°C. This makes it an ideal chemical store for renewable energy. There is an existing distribution network, in which ammonia is stored in large refrigerated tanks and transported around the world by pipes, road tankers and ships.
- Zero-carbon fuel – ammonia can be burnt in an engine or used in a fuel cell to produce electricity. When used, ammonia’s only by-products are water and nitrogen. The maritime industry is likely to be an early adopter, replacing the use of fuel oil in marine engines.
- Hydrogen carrier – there are applications where hydrogen gas is used (e.g. in PEM fuel cells), however hydrogen is difficult and expensive to store in bulk (needing cryogenic tanks or high-pressure cylinders). Ammonia is easier and cheaper to store, and transport and it can be readily “cracked” and purified to give hydrogen gas when required.
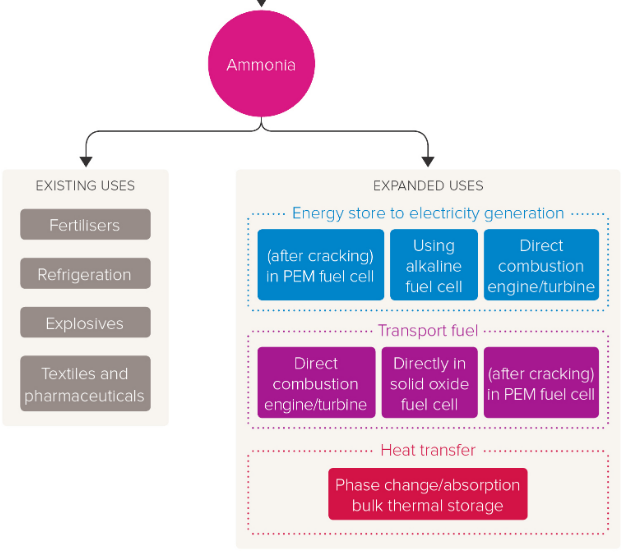
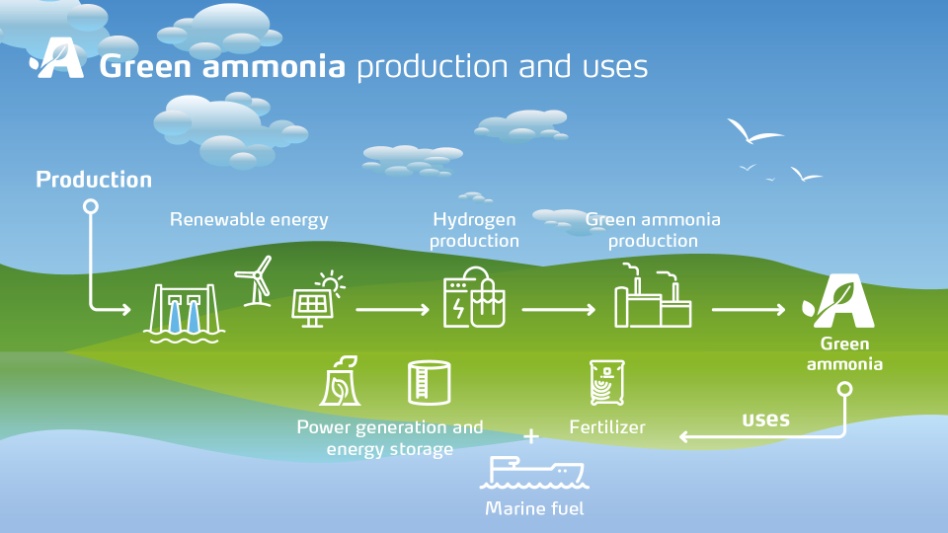
Must Read: https://www.iasgyan.in/blogs/green-hydrogen-an-overview
https://epaper.thehindu.com/Home/ShareArticle?OrgId=G8I9RTDMP.1&imageview=0
1.png)